Princeton is famous for scientific innovation, but few people know that the University runs one of the most efficient power plants in America.
The plant, an unassuming structure just south of the MacMillan building on Elm Drive, was built just to power campus. It is a marvel of energy efficiency, providing both electricity and heat to every dorm and classroom at Princeton.
And for Ted Borer, the University's Manager of Mechanical Systems, it is a passion.
When Borer arrived on campus in the summer of 1994, the plant existed only on paper. Two years later, a finished plant was producing its first electricity. By the middle of 1997, it was steadily online, continually producing power for the campus. Along the way, Borer managed construction of the plant, made sure that a staff was prepared to operate it, and above all saw to it that the plant would meet Princeton's needs.
He had to juggle the competing demands of the engineering firm that had been hired to construct the plant, the University workers who needed to be able to maintain it once it was built and the architects who had designed it in the first place. His concerns ranged from the plumbing that would support the plant's main engine — a powerful turbine originally designed for lifting airplanes — to the locks on the doors. At the end of the day, it was his job to make sure that the University had a functioning power plant.
At the same time, he had to worry about inking contracts with local utilities to assure that the University could buy extra power if the new plant was not enough, and getting all the permits needed to run the plant.
"It was really good, really exciting, really challenging," he explained in an interview Monday. His office walls are covered with engine diagrams and maps showing the location of steam pipes. Graphs of campus power use crowd his desk.
During the construction phase he was kept constantly busy. "I really didn't have a lot of free time," he said.
But the intense effort was a labor of love. "I started out building train sets and tree houses," he said, noting that he has always enjoyed figuring out how things work. "It's a dream for someone who does project management to take on something like that," he said.
Like a turbine on a jet plane, the one at the core of a typical power plant has a series of fans linked together in an airtight chamber. Each successive fan drives the air through more rapidly than the last.
After air shoots through the fans, it is mixed with natural gas and ignited. It expands, turning the turbine and generating electricity. This process generates usable electricity, but it is inefficient.
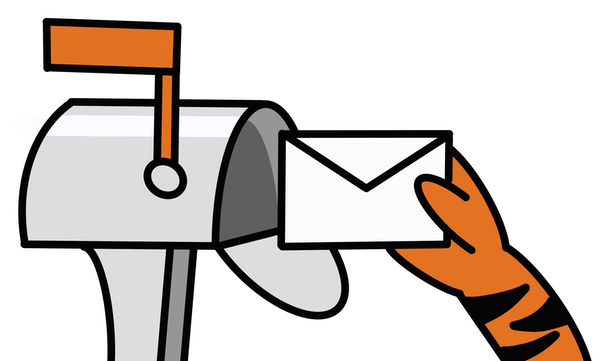
Less than half the energy involved actually ends up turning the turbine — the rest is released as heat. This heat is usually radiated into the air or into the water of a nearby river, without being put to use.
Princeton's plant, though, is different. The hot gas pushed out of the turbine as it spins is allowed to flow by a network of pipes that contain water, turning the water into steam. The steam is then sent through a vast network of underground pipes, warming buildings all over campus.
This makes Princeton's facility a "cogeneration" plant — it generates both electricity and useful heat at the same time. Most power plants — ones that cannot use their leftover heat — are only 25 percent efficient, but the University plant, heating buildings as it powers the campus, is fully 75 percent efficient.
The plant works like a mechanical heart to warm the campus. One set of pipes, like arteries, takes pressurized steam out to every corner of campus. Once the steam has been allowed to flow through a building, spreading its heat and condensing back into water, a parallel set of pipes — like a system of veins —carries water back to the power plant.
The plant runs 24 hours a day, 365 days a year. At peak power use times — the middle of the day, particularly in the summer – the campus plant cannot meet demand, so the University buys power from a local power company. Our local plant is "synchronized" with the electricity grid, allowing us to draw extra power without interrupting the flow of electricity to campus.
Why did the University bother to build its own plant, instead of just buying electricity like everyone else?
"The motivation is economic. Unabashedly, it is about saving money," Borer explained. "We can make electricity cheaper than we can buy it."
Though the University pays all the plant's costs, it still manages to save money relative to the cost of buying electricity. Now that the plant is built, Borer works on making the University's power use more efficient.
This summer, he introduced motion sensors that keep vending machines from running when no one is around, a measure he said will save up to $20,000 a year.
"Over the life of the plant, we're projecting saving three to five million dollars a year," Borer said. The plant will probably last around thirty years, he noted.
Borer's commitment to energy efficiency extends beyond his job. On his wall, along with the technical schematics, is a copy of newspaper story about his unusually efficient commute. Every day, he travels eight miles from his home to work on a bicycle.
He explained that cost savings go hand in hand with environmental benefit.
"This is the thing I feel really good about – we're making a huge reduction in environmental impact while saving the trustees a lot of money" by running an efficient plant, he said.