Thanks to a team of University researchers, however, those size limitations may soon be outdated. Nature Nanotechnology published an article by electrical engineering professor Stephen Chou and Qiangfei Xia GS ’07 on their new method of enhancing the quality of tiny features on microchips with great precision.
“When you make structures very small, you are limited by the noise — the statistical nature — of the process,” Chou said.
Computers have been shrinking since they were first introduced in the 1940s. The invention of the microchip in 1959 enabled one of the first significant decreases in computer size. Today, most microchips range from several to several hundred square millimeters and can be found in computers, cell phones and even implanted in pets.
Microchips are made using electrons and photons to carve dot- and line-shaped ridges into metal. The process is not perfect. Electron and photon motion is random, producing noise that causes imperfections in the ridges.
The effect of noise is compounded as the size of chips decreases. Imperfections can significantly lower the chips’ quality, reducing the effectiveness of the devices made from them.
Previous attempts to correct the flaws focused on improving the quality of microchips during the production process, Chou said.
“We recognized that we had to take a completely different approach,” he explained.
Self-perfection by liquefaction, the technique developed by Chou and Xia, is implemented after the microchips are produced. “We remove defects in the last step and can smooth out roughness on the nanometer scale,” Xia noted.
The process uses a laser similar to those used in laser eye surgery to melt the ridges on the surface of the microchip. The ridges are melted for less than a millionth of a second, allowing them to temporarily liquefy.
“We used a laser pulse to simply melt the nanostructures, and the surface tension makes them more rounded,” Xia said.
When the liquid solidifies, it becomes metal ridges, but the ridges are straighter and the dots are rounder.
This effect could not be achieved by heating the ridges until they melt, as is done to plastic structures. To melt the metals, the microchip would need to be raised to temperatures at which the entire device would melt.
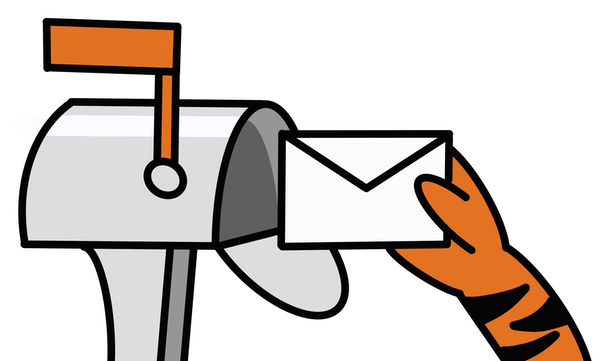
Chou and Xia were able to further modify the shapes of the ridges and dots by placing a quartz sheet over the melted sections, which caused them to assume the shape of a rectangular prism.
An unexpected result the team found was that placing the quartz a slight distance above the liquid metal caused it to rise before solidifying. This results in taller and narrower features on the surface of the chip, enhancing its quality.
“When two dissimilar materials are brought close together, there is always a potential difference; there is always a charge difference,” Chou explained. This charge difference applies a force to the liquid metal, raising it.
Chou and Xia’s technique was able to smooth the defects to an extent beyond what people thought possible using today’s technology. Currently, reducing defects to three-nanometer-wide ridges is considered ideal, but the new technique is able to reduce them to a size much smaller than that, Chou said.
“Our technique will enable developers to create better performance nanochips,” Xia noted.
Xia added that many microprocessor manufacturers, including Intel, have contacted them about their research. Devices like central processing units, which contain microchips, could be made smaller and more efficient using the process.
While Xia now works for Hewlett-Packard, Chou will continue trying to enhance the technique and plans to test it on an eight-inch wafer.
“We push for understanding the fundamental principles of the process, which will help to enhance the technology further,” he said.