The U.S. Navy was looking to heat up its research in the electric power industry earlier this year. And it did not need to look much further than Princeton material science professor Anthony Evans.
With a five-year, $5-million grant, the Office of Naval Research is funding a collaboration led by the University professor that is meshing the intellectual power of six universities and the production capacities of several private companies to increase the reliability of gas turbines.
As the director of the research consortium, Evans — who is also the director of the material science and engineering program — is heading the efforts to develop materials that will perhaps allow gas-fired electric power plants and jet engines to run at temperatures that are 200 degrees higher than currently possible.
If the consortium is successful, the turbines in jet engines and gas-powered electric plants will be able to run much more efficiently and hence release fewer pollutants into the environment, Evans said.
Gas turbines work to generate energy by combusting natural fuels — a process that, if efficient, yields only water, carbon dioxide and vast amounts of energy and heat. However, because these turbines are restrained by the durability of their parts, they cannot operate at the high temperatures required for complete combustion. This means the power generators and engines that use gas turbines must spend energy to cool the turbines and therefore cannot fully process the natural fuel — which is an inefficient and wasteful process that can lead to the formation of environmental pollutants.
The turbines run at temperatures that are higher than the melting points of their metal parts because they use a thermal barrier coating that protects the parts from high temperatures. However, even these coatings have their limits — they tend to flake off at temperatures higher than 1,200 degrees Celsius and expose the metal to the heat.
The research consortium is hoping to raise that ceiling to 1,400 degrees Celsius, an effort that could go a long way toward reducing both the need for natural fuels and the amount of environmental pollutants produced.
The consortium started work only four months ago. But the scientists have already written a paper explaining the mechanisms by which the thermal insulators fail. They have also developed a new bond coat that helps to keep the thermal insulator attached to the metal parts, Evans explained.
Daniel Mumm — a staff member who is researching the thermochemical performance of the materials — said, "Ultimately, our goal is to dramatically increase the reliability of thermal barrier coatings and gas turbines."
Just as the lid of an icebox must be kept closed to keep the ice frozen, so must the thermal insulators stay attached to the metal parts to keep them from melting.
The ceramic materials currently used to protect the metal parts are strong thermal insulators, Evans explained. Ceramic materials are defined as inorganic and nonmetallic solids that are formed by bonds between metallic and nonmetallic elements, one of which is usually oxygen.
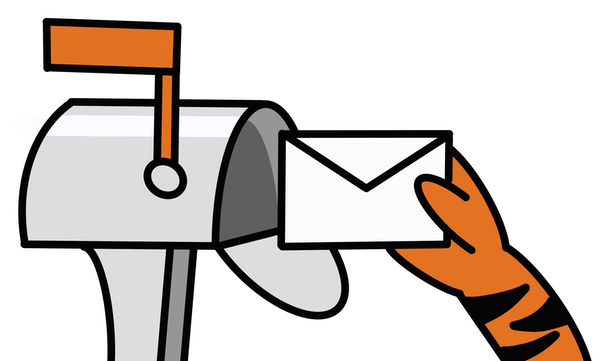
Zirconia, a ceramic that is composed of a rigid structure of zirconium and oxygen atoms, is the ceramic of choice, Evans said. "Zirconia does work, but we want to make it better," he explained.
Evans, who earned his Ph.D. in metallurgy at Imperial College, London University in 1967, said ceramic materials are the insulators of choice because they conduct heat poorly. In addition, they have melting points that are often higher than 2,000 degrees Celsius, well above the 1,200 degrees Celsius where gas turbines currently operate.
They are also not heavy solids and resistant to corrosion and stress. Because they have this combination of lightness and high melting points, ceramic materials are also used to coat the surfaces of space shuttles to prevent them from burning upon re-entry into the Earth's atmosphere.
However, ceramic materials are very brittle because their atoms are packed so tightly that they cannot move across each other, which would allow the material to bend. Therefore, when ceramic materials are struck, they shatter into pieces. This is problematic because regions of the ceramics are exposed to particle impact and foreign object damage during the combustion of fuels. In addition, because of the way the atoms are packed, it is difficult to manufacture ceramics that are free from defects.
Furthermore, the ceramic materials and the metal parts expand at different rates as temperatures increase. As a result, spinels — or cracks — tend to form between the ceramic and the metal parts, causing the coating to flake off. This makes it difficult for the coating to stay attached and protect the metal from the heat. Evans explained that part of the universities' role is "to determine how the ceramic stays attached."
Mumm, who came to Princeton in 1999 five years after earning his Ph.D. in materials science and engineering at Northwestern, added that he and his colleagues are looking to improve the materials "by understanding from a scientific basis the mechanism by which thermal barrier coatings ultimately fail."
To focus on these problems, the consortium is testing many different types of ceramic materials and engineering some of the more promising ones to improve the physical properties. It is able to test these new materials through a process called "thermal cycling."
As postdoctoral fellow Stefanie Chiras explained, "We put it in a furnace, take it from room temperature to a high temperature and then we bring it down. We do about 200 cycles between room temperature and 1,100 degrees Celsius to 1,300 degrees Celsius."
Evans added, "We keep raising and lowering temperatures to see how long they last."
Princeton does not currently have the machinery to conduct these tests — they are carried out at General Electric, which makes the parts. Chiras said, "It's a very collaborative effort between the industry and academia" with the universities conducting the theoretical, experimental and analytical research while the companies provide some equipment and produce the actual parts.
The consortium is the brain child of Evans, who originally conceived the project.
"I wrote the proposal for the research, and I asked people who would be able to do it," he said. The people he approached were "people I knew in the past," and they were more than willing to participate, he added.
Because he used to work at the University of California at Santa Barbara and then at Harvard before coming to Princeton in 1988, Evans had several contacts at these institutions. In addition, Case Western Reserve University, the University of Pittsburgh and the University of Virginia have participated in the consortium.
It was also through connections that Chiras became involved with the project — she earned her master's degree and Ph.D. at Santa Barbara.
Princeton researchers also involved with the consortium are mechanical and aerospace engineering professors Zhigang Suo — who does computer models and calculations to explain the mechanical behavior of thermal insulators — and Winston Soboyejo who helps with the experimental research.
The consortium meets for two days every six months. It last met this past September for a three-day workshop.
Evans expects the research consortium to continue to run on high heat for the next few years. "Within five years, we hope to make a lot of progress, followed by a leveling-off," he said. And they have no intention of cooling down any time soon.